Example of the production process using SCHÜMER SECAN® cotton
A brief overview of the production stages illustrates modern and high-quality fabric production for reliable protective workwear. Cotton itself is known for its superior comfort and high level of breathability. These advantages are combined in flame-retardant SCHÜMER SECAN® cotton to provide optimum protection. This creates an efficient, extremely user-friendly product solution.
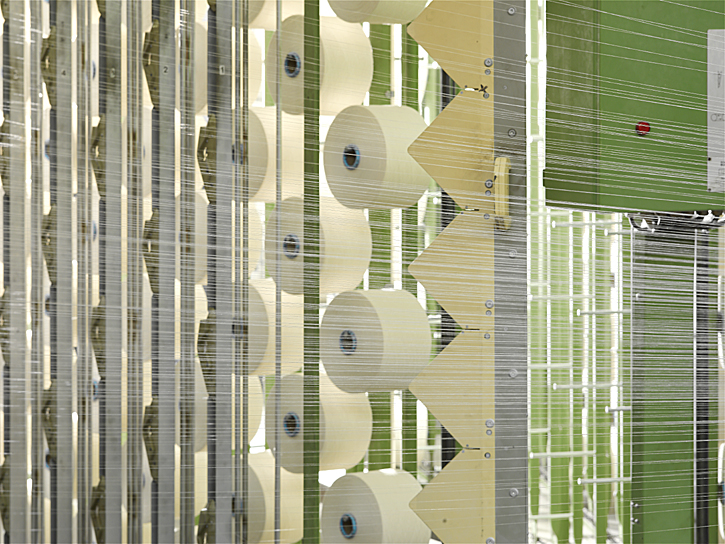
Preparation
The yarn is prepared for the subsequent weaving process. The emphasis is on the warp production. There are two methods: sectional warping and warping. During the sectional warping, approx. 5,000 threads are parallelised and wound on a warping drum. Following this, the web warp emerges. During the warping, approx. 600 threads are parallelised and wound on a warping drum. Several warper beams, usually 10 pieces, go through the sizing machine together afterwards. During the sizing process, the threads are soaked in a substance, a sizing agent, which smooths the threads for the weaving process and increases their abrasion resistance. At the end of the sizing machine, the threads of the warper beams are combined into a warp.
Weaving
Weaving is one of the oldest known processes for producing textile fabrics. At least two thread systems, the warp and the weft, are crossed at right angles, and the warp yarns are prestressed in the weaving machine forming the support into which the weft threads are successively inserted from one selvedge to the other through the entire weaving width. This technique has not changed in the more than 400-year history of the weaving machine. What has changed for the better, is the working speed. One hundred years ago, for a production width of 2 meters, approx. 100 rounds per minute were entered into to the warp; today it is approx. 1,200 rounds per minute.
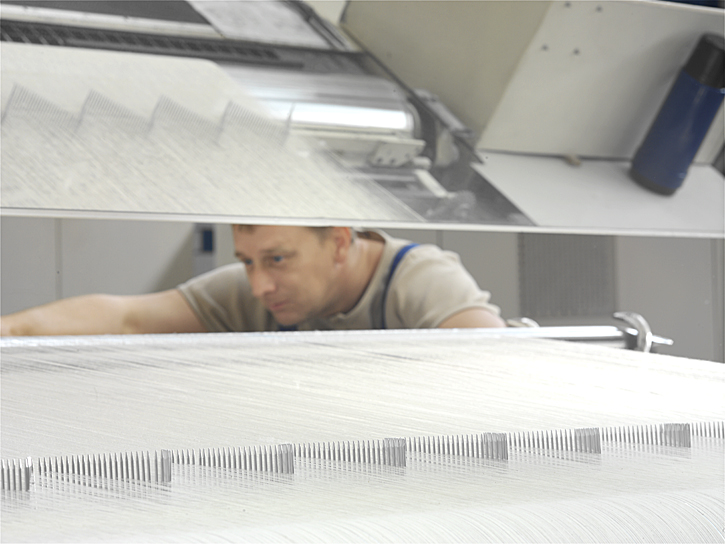
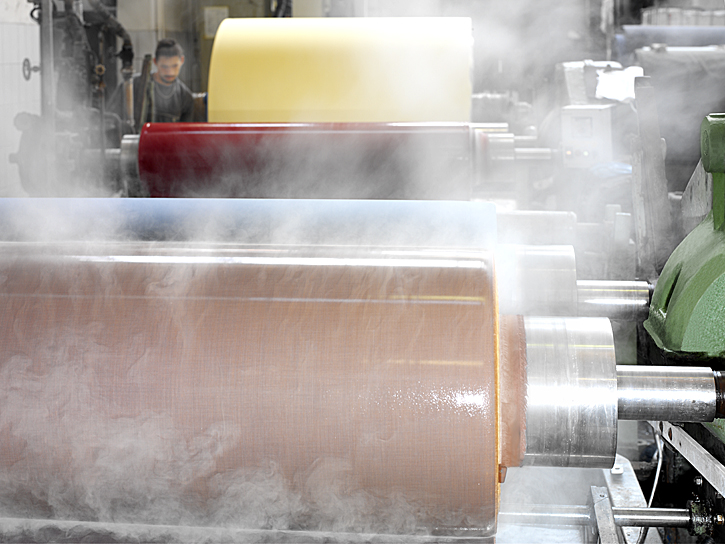
Dyeing
During the dyeing process, the textile material is coloured by applying colourants. Dyeing can be carried out almost anywhere during the textile processing chain: on fibres, yarns or fabrics. Fabric dying distinguishes between two methods: With batch dyeing, an exhaust process, fabric is passed through a dye bath where dye is dissolved or dispersed in the water. With continuous dyeing, known as padding, uniform wetting of the fabric with dye takes place over the entire fabric width by squeezing it between hard rubber rolls.
Finishing
Finishing is the collective term for procedures carried out on fabrics, yarns and fibres. It often follows the actual creation process of the raw fabric. Finishing optimises the properties of the material and its practical value with respect to intended use, such as appearance, wear and care behaviour, durability and flame retardancy. A distinction is made between chemical, mechanical and thermal processes. Depending on requirements, there are up to 20 finishing steps between raw and finished fabric, including dyeing. The SCHÜMER SECAN® manufacturing process is based on equipment unique to Germany, which allows individual adjustment.
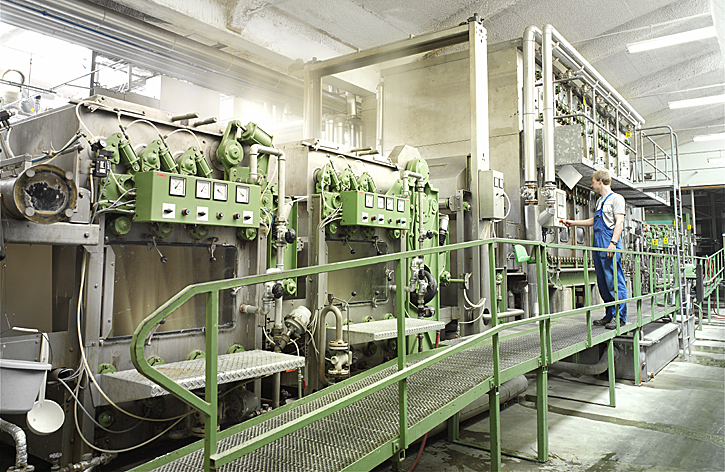
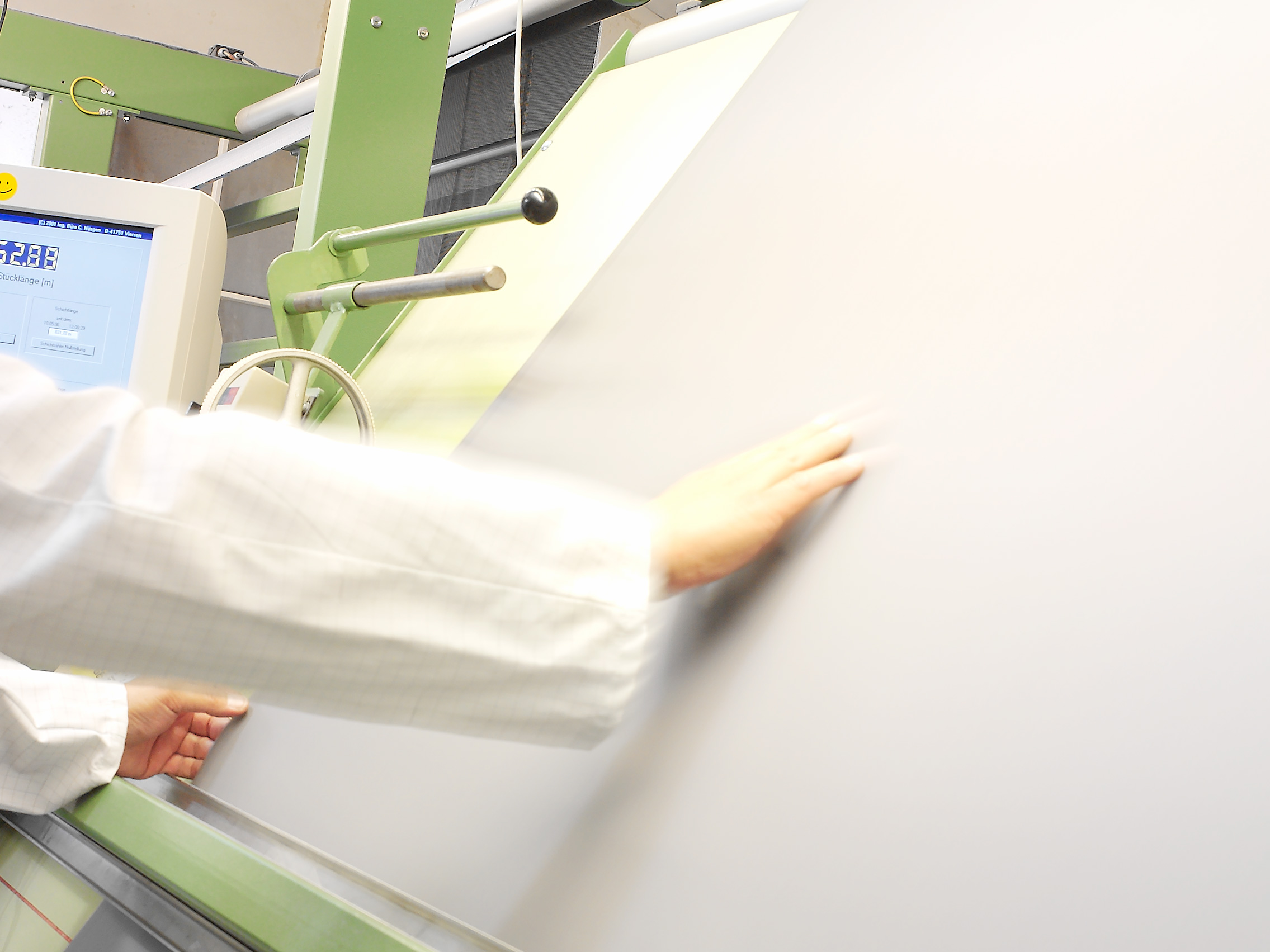
Checking
In order to be able to guarantee consistent quality of textile products inspections must be carried out frequently. The most important test is the finished goods control, which takes place after finishing. Depending on the product and customer requirements, the required tests are carried out according to specified standards, in the company’s own laboratory or external test institutes. Further checks at the beginning and during the creation process help to detect product defects at an early stage. This improves product quality and reduces the cost of troubleshooting and rejects.
Testing
Fabric with specific requirement profiles must undergo special tests. SCHÜMER SECAN® cotton fabrics offer state-of-the-art protection for workers at fire and heat-sensitive workplaces. In addition to the European EN standards required by law, SCHÜMER SECAN® must also comply with the previously applicable DIN standards and the SCHÜMER SECAN® standard, which we have specially developed for this purpose and which exceeds the current European standard by far. Close inspection takes place every 100 to 120 meters of production in an independent external testing institute.
Only the last sample of the three, which passes the SCHÜMER SECAN® flame test, is actually the unique SCHÜMER SECAN® fabric.